When Scienco/FAST says its water treatment systems are meant to last, the company is talking in decades.
The average product life for a FAST marine system is 30 years, said Bob Millerbaugh, Scienco/FAST executive vice president–sales and marketing.
The company, founded as a part of St. Louis Shipbuilding—former owner of the Federal Barge Line—in St. Louis, was the first to manufacture marine sanitation devices (MSDs) back in the late 1960s.
By 1969, the first prototype FAST—standing for Fixed Activated Sewage Treatment—system was installed on a towboat, the mv. Missouri, while the vessel was underway.
Long History
MSDs were the solution to a very big problem in those days. The Environmental Protection Agency was getting complaints from citizens about cruise ships and cargo ships that would pull into ports and dump their sewage, which would wash ashore. The United States was considering the Clean Water Act, and it contacted the U.S. Coast Guard to ask about a sewage treatment solution that would work on the nation’s waterways.
By 1973, after years of successful operation aboard three towboats, FAST unit sales and production began. Even though there were no federal rules before 1975, towboats operating on the rivers had to meet individual state regulations.
By 1975, the U.S. Coast Guard began regulating MSDs, requiring them to be tested and certified. FAST testing was done aboard the towboat the mv. United States while underway, and the unit passed all tests and was certified.
Quality Tested
While regulations say such systems must meet testing standards for at least 10 days, the FAST system is built to do so day after day for as long as the unit is in operation.
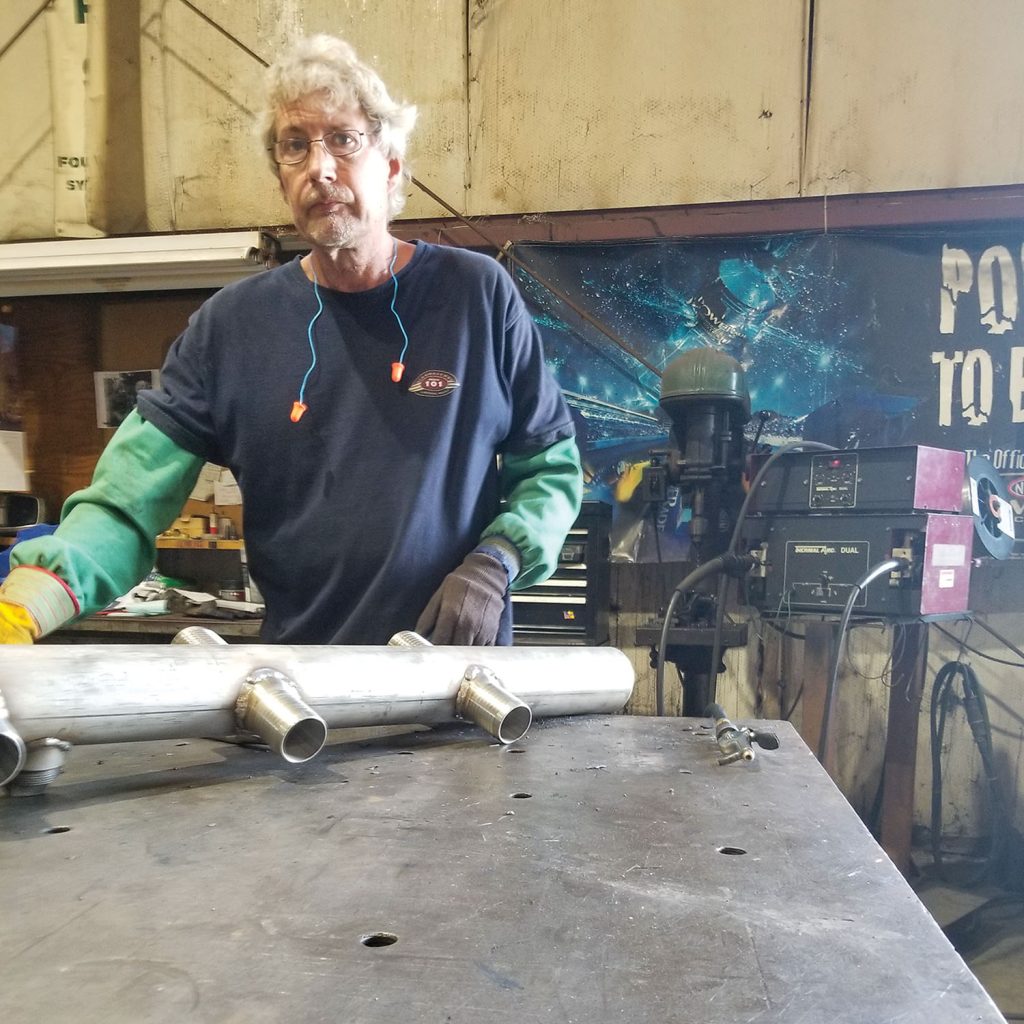
“It doesn’t matter if it’s 10 days or forever,” Millerbaugh said. “That’s what sets us apart, and that’s why we do business with all of the big people.”
Those “big people” include the U.S. Navy, U.S. Coast Guard and navies and coast guards from nations around the world, along with companies well known to the inland waterway community like ARTCO, American Commercial Barge Line, Ingram Barge Company and Kirby.
FAST systems have been installed on towboats, tugs, offshore supply vessels, diving support vessels, submersibles, military war ships, offshore platforms, drill ships, crane barges, pilot boats, shop and office barges, container ships, tankers, bulk carriers, research vessels, ice breakers, survey ships, school ships and cruise ships, to name a few.
FAST remained part of St. Louis Shipbuilding until 1985 before being sold to Smith & Lovelace. That company was then acquired by BioMicrobics, which also builds land-based water treatment systems under the BioMicrobics name. The result is that FAST product developers have access to engineers and researchers that can help produce custom products for any need, along with its three different off-the-shelf product lines that treat water as needed for one person up to 780 people.
Among the most recognizable products are marine sewage systems (LX, MX, DV and MSDs); built-in, custom-made systems; ballast water treatment systems; PortaFAST, a complete dock restroom with MSD; and SaniLIFT, a lift station.
“Our systems have been tried and tested,” Millerbaugh said. “We’ve been in business 53 years doing marine sewage treatment.”
American-Made Commitment
While the company and the product line have both grown over the years, its values have stayed the same. That includes a commitment to building quality products, which is why Scienco/FAST does all its own manufacturing. Welding, assembly, painting and shipping all take place at the company’s 20,000-square-foot factory in Fenton, Mo., just outside of St. Louis. Two of the FAST division’s nine employees have been on the payroll for more than 50 years.
Jim Predeau, general manager, is the longest tenured employee, serving 52 years. He started with Scienco/FAST in 1970, briefly leaving to serve the country in the armed forces during the Vietnam War, and then returning to the shipyard. He left again in 1987, but later returned to run the entire operation.
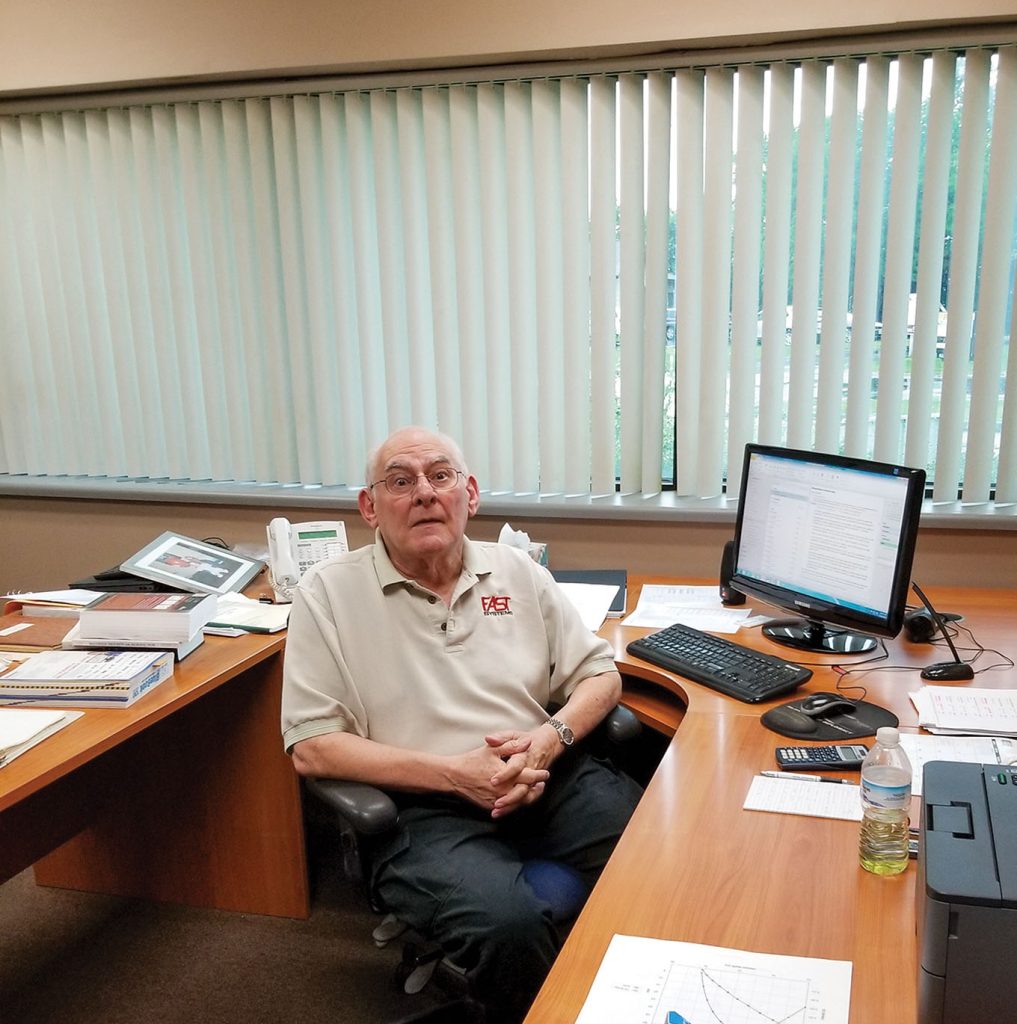
Alan Fleischer, vice president of engineering, has been with the company 50 years. Coming on board in 1972, he was instrumental in the design and implementation of FAST. He led the company during its time as part of Smith & Lovelace, heading the division then, and then later lead Scienco/FAST as president. While now retired as president, he still comes in part-time, providing invaluable experience to the team.
Other longterm employees include Art Page, manager of shipping and receiving, who has 40 years with the company, Steve Carpenter, vice president of engineering, with 33 years of service, and Mike Erxleben, lead welder, who has been with Scienco/FAST for 20 years.
Many of the products those employees made are still in operation.
“We like to say we have more than 4,800 [heavy marine and offshore use] systems working that we have sold since we started,” Millerbaugh said.
The company also services its products worldwide.
“We could be in Shanghai one week and then off the coast of France the next week for another one,” he said.
If a part does fail, Scienco/FAST also manufactures replacement parts.
Continued Innovation
But while the same technology has worked well all these years, the company continues to innovate. New initiatives include redesigning some of the largest tank systems to make them lighter and more efficient. The company also recently developed a marine bio-membrane reactor (MBR) that is adapted for marine use. Previously, the products were available only in Europe, Millerbaugh said.
MBRs recycle waste to allow for water that is 99.9 percent clean. While not useful for drinking water, it can be used to wash down decks or power cooling systems, lessening the amount of water that must be carried aboard a vessel.
Scienco/FAST is also working on a new, smaller and more cost-effective plastic system made with tugs in mind, Millerbaugh said. It is designed to be an economical, yet long-lasting option.
Caption for top photo: Scienco/FAST’s marine water treatment systems have an average product life of 30 years. The company has been in business more than 50 years and welds, assembles, paints and ships products from a 20,000-square-foot factory in Fenton, Mo. (Photo courtesy of Scienco/FAST)